Some Important Characteristics Of Textile Fibers
The materials which consist fibrous structure and its length is thousands times higher than its width and which can be spun into yarns and suitable for weaving and knitting is called Textile fibers.
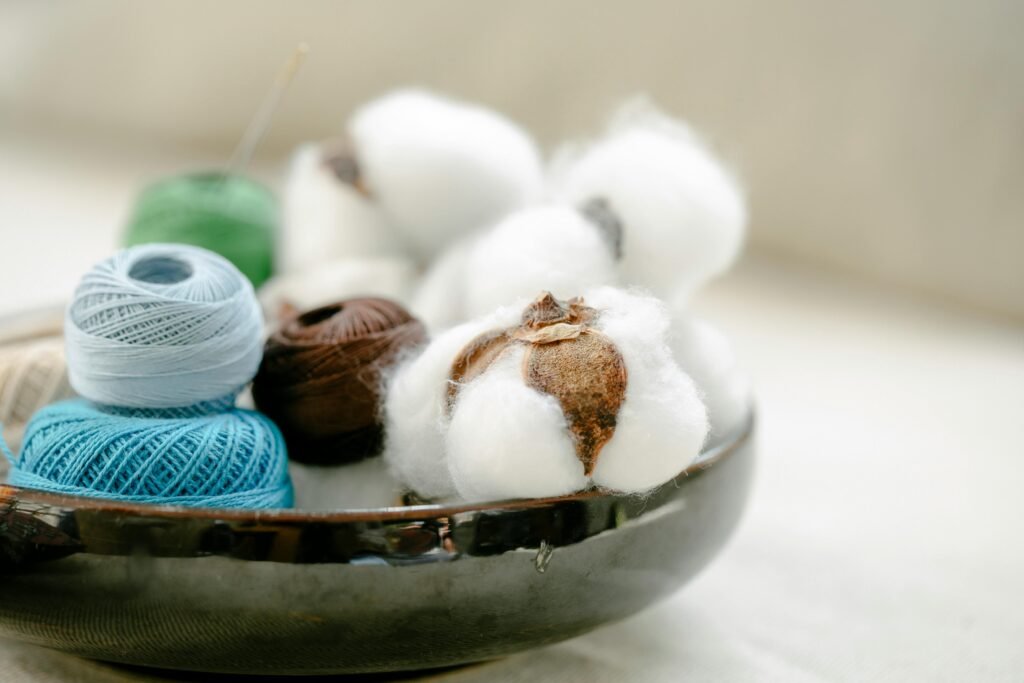
To become a textile fiber, it should have the following fundamental properties. These are:
- It must have sufficient strength, elasticity and spinning power.
- It should have fibrous structure and the length should be thousand times longer than its width.
- It should have fine structure and flexibility.
- It should have dye ability or dyes and chemical absorbency.
- It must be readily obtainable in adequate quantities so that the end products will be cheap.
- Protecting ability from biological agents.
Some Important Characteristics of Textile Fibers
Essential Properties
- Length to width ratio
- Strength
- Flexibility
- Cohesiveness
- Uniformity
Other Properties
- Physical shape
- Specific gravity
- Luster
- Moisture regain and content
- Elastic recovery
- Elongation
- Resiliency
- Resistance to thermal behavior
- Resistance to chemical
- Resistance to biological agents
- Resistance to environmental condition
Some Important Properties of Textile Fiber are discussed:
Length To Width Ratio: Fibrous material must possess adequate staple or fiber length and the length must be considerably higher (1000 times) than the width of the fiber.
Length To Width Ratio of Some Typical Fiber as follows:
Fiber | Length To Width Ratio |
Cotton | 1400 |
Wool | 8000 |
Flax | 1700 |
Silk | 33 x 10E4 |
But to be a fiber, the staple length must not be less than ½ inch.
Strength: Strength of any material is determined by the breaking strength (that is tenacity strength) which express as force per unit cross-sectional area. With this term (strength/tenacity strength) we may describe the ability of a bundle of fiber or yarn to resist breakage under tension/load.
Tenacity: According to ASTM (American society of textile manufacturers), the tensile strength when expressed as force per unit linear density is called tenacity. Tenacity is determined by applying a force to a known unit of fiber and measuring the force to break the fiber.
Tenacity = Breaking load/ mass per unit length
Tenacity expresses as grams per tex (gtex) or grams per denier (gd).
Tenacity of Some Common Fiber
Fiber | Grams Per Denier |
Raw cotton | 3.0-4.9 |
Jute | 3.0-5.8 |
Flax | 2.6-7.7 |
Ramie | 5.5 |
Silk | 2.4-5.1 |
Wool | 1.1-1.7 |
Hemp | 5.8-6.8 |
Flexibility: It is one of the essential property of textile fiber. The fibers should be sufficient by pliable, then only it can be wrapped around another fiber during spinning.
Cohesiveness: It may also be termed as spinning quality of fiber. It is the property of an individual fiber by virtue of which the fibers are hold on to one another when the fibers are spun into yans.
Uniformity: It may describe the similarities in length of fiber which are spun into yarn. To make a good quality yarn, it is important that the fibers must be similar in length and width in spinning quality and in flexibility. There is no problem in producing uniform man-made fibers but for natural fiber uniformity is difficult to achieve. So, for natural fiber it is essential to blend many batches in order to manufacture good quality yarn and fabrics.
Physical Shape: The shape of fiber has good impact on the other properties of the fiber. It affects the surface irregularities and cross-section of the fiber. Thus, it affects the properties of the produced yarn and therefore the fabric.
Specific Gravity: The specific gravity of a fiber indicates the density relative to that of the water at 4°C. The specific gravity of water at 4°C temperature is 1per cubic centimeter or pounds per cubic foot. Fabrics which are composed of higher specific gravity are heavier than that of the fabrics produced from fibers of lower specific gravity.
Specific Gravity of Some Selected Fibers:
Fiber | Specific Gravity |
Cotton | 1.54-1.56 |
Flax | 1.50 |
Jute | 1.48 |
Silk | 1.34 |
Wool | 1.30-1.38 |
Ramie | 1.51 |
Hemp | 1.48 |
Glass | 2.54 |
Asbestos | 2.10-2.80 |
Viscose rayon | 1.52 |
Nylon | 1.14 |
Lusture: Luster refers to gloss or shine that a fiber possess. It is actually the amount of light reflected by the fiber and it determined the fibers natural brightness and dullness.
The natural fiber silk has the high luster while another natural fiber cotton has low luster compare to silk fiber. Man-made fibers are manufactured with controlled luster.
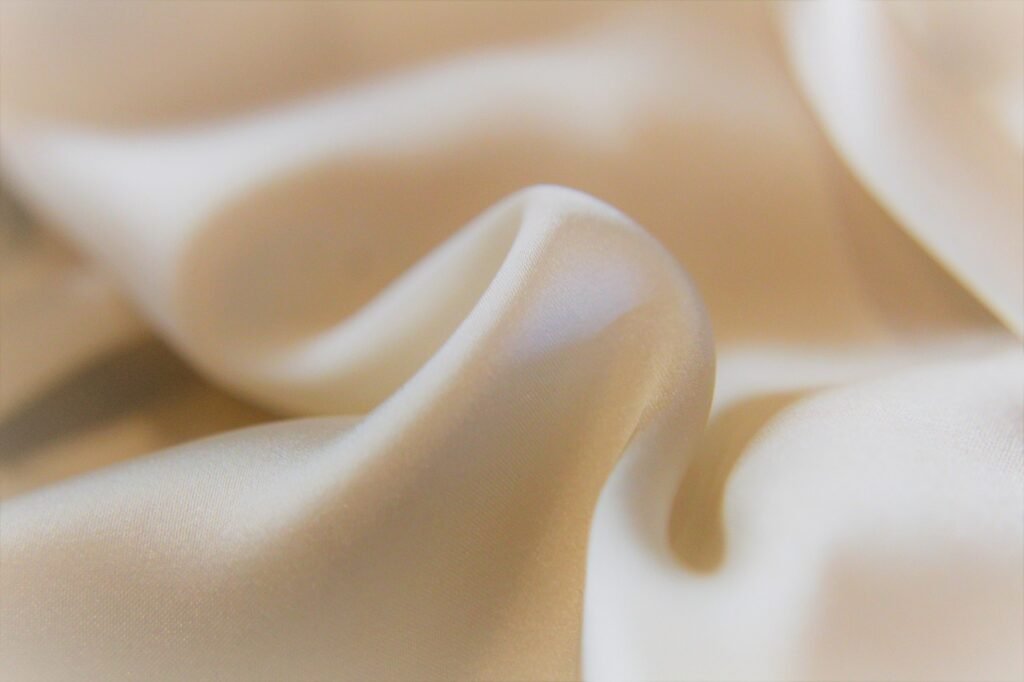
Moisture Regain and Moisture Content: Textile fibers generally have some contain amount of water as an internal part of their structure. This is because of the humidity present in the nature atmosphere.
Fibers with good moisture and moisture content will accept dyes and chemicals more readily than fibers with low regain. A few fibers have regain and thus it creates problems relative to processing.
Again, the relation of the fiber strength to moisture content is an important consideration in the evaluation of fiber behavior. Some fiber are stronger when wet than dry, some are weaker when wet than dry and some shows no change. Therefore, the maintenance of textile products are influenced by the strength regain relationship.
Some Moisture Regain of the Common Fibers:
Fiber | Regains at 75°F and 65% Relative Humidity | Regains at 70°F and 95-100% Relative Humidity |
Raw cotton | 8.5 | 15 |
Mercerize cotton | 10.3 | – |
Silk | 11 | 25 |
Wool | 16 | 29 |
Acetate | 6.5 | 14 |
Viscose rayon | 11.5-16 | 27 |
Elastic Recovery: Elastic recovery is the percent to return from elongation towards its original length. If a fiber returns to its original length from a specified amount of attenuation, it is said to have 100% elastic recovery at x-present elongation. The elasticity or elastic recovery of a fiber is determined by several aspects like what type of load is applied and how many times it is held in the stretched position.
Elongation: When a fiber is subjected to a force it will stretch to a certain degree. The stretching is described as the elongation or extension. It may be measured either as an elongation under certain load or an elongation reached under the fiber breaks. Elongation expressed as percentage.
Breaking Elongation and Elastic Recovery of Some Common Fibers:
Fiber | Dry Elongation | Percentage of Elastic Recovery at X-Percent |
Cotton | 3-10 | 74 at 2% |
Flax | 2.7-3.3 | 65 at 2% |
Hemp | 1.8 | – |
Jute | 1.7-1.9 | 74 at 2% |
Silk | 13-25 | 70 at 2% |
Wool | 20-40 | 99 at 2% |
Resiliency: Resiliency is the ability of fiber to bounce back or return to its shape following compressions, bending or similar deformations. Resiliency is important to determine the crease recovery of a fiber or fabric.
Thermal Behavior: The behavior of fibers on heating has real importance, particularly with in the range of temperatures, which are met in practical use. Fabric should be withstand the temperatures used in processing, drying, ironing without undue deterioration. Flammability of fiber has also great importance during its use. Generally synthetic fibers are more flammable than the natural fibers.
Resistance To Biological Agents: Some fibers basically for natural fiber, they are destroyed by the biological agents. So, the fibers must be able to protect themselves from the destructive effects of the biological agents.
Resistance To Chemical: Processing of fibers, yarns and fabrics often involve the use of chemicals of great variety like bleaching agents, detergents, alkalis, acids, dyeing and finishing.
Assistances and other chemicals are used in preparing the finished textile. The fibers must withstand these substances without suffering harmful effects.
Resistance To Environmental Conditions: Many of the times the finished textiles are in contact with the environment such as sunlight, UV ray, rainfall etc. Besides these the wind in different seasons contains different elements. So, the fibers used in different seasons must be preferable with the environment and have to withstand the various environment conditions with suffering much.